GRE and FRP Lamination Safety Tips for Field Installers
GRE FRP lamination is a precise and critical operation performed in the field, requiring strong technical skill and strict adherence to safety standards. Field installers not only work with abrasive materials and resins but often do so in challenging site environments, making safety an essential focus at every step.
This guide provides practical, field-ready safety tips, combining best practices from manufacturers and professional site protocols used in Fiberglass pipe installation.
Personal Protective Equipment (PPE) Is Non-Negotiable
Field lamination exposes workers to fiberglass dust, chemical vapors, and heat. The proper use of PPE significantly reduces risk. Installers must always wear:
- Chemical-resistant gloves
- Safety goggles or full-face shields
- Dust masks or P100-rated respirators for fiberglass dust
- Coveralls to prevent skin contact with fibers and resins
- Safety boots and hearing protection when using FRP pipe tools.
Ensure PPE is clean, undamaged, and suited for the specific materials being handled.
Maintain a Clean and Controlled Work Area
A tidy workspace reduces slip hazards, prevents contamination of materials, and improves workflow efficiency.
- Organize FRP pipe tools before starting
- Avoid placing resin-soaked materials on the ground
- Keep fire extinguishers and first-aid kits nearby
- Cordon off the lamination area if in a shared workspace
Safe Handling of Resins, Hardeners, and Solvents
GRE/FRP lamination uses reactive chemical systems that require correct storage, handling, and mixing:
- Store chemicals in clearly labeled, sealed containers away from direct sunlight
- Use calibrated measuring tools to mix resin, hardener, and accelerators
- Never mix components by eye or guesswork
- Do not use acetone to wash skin—use soap and water
- Ensure all mixing is done in well-ventilated areas
Spill response kits should always be available on-site, especially for large Fiberglass pipe installation projects.
Control of Dust and Fumes
Surface preparation (like sanding) releases fine fiberglass particles, while curing resins can emit hazardous fumes. Mitigation is key:
- Prefer wet sanding over dry sanding to reduce airborne fibers
- Use dust extraction units when grinding
- Wear P100 filters or equivalent masks when dry sanding
- Provide mechanical ventilation or fume extraction in enclosed areas
These steps are essential when preparing joints for GRE/GRP tapering or lamination
Surface Preparation and Joint Fit-Up
Proper lamination starts with preparing the spigot and socket correctly:
- Sand off 0.3–0.6 mm of the resin-rich surface layer with P35–P40 abrasive
- Remove all dust with a clean brush or cloth
- Check alignment and ensure pipe gaps are within tolerances (e.g., 1–3 mm for DN<600)
- Mark the shaving length and overlap clearly
Avoid laminating wet or contaminated surfaces—moisture will compromise the bond.
Environmental and Weather Considerations
Lamination success is sensitive to site conditions:
- Ensure ambient and surface temperatures meet the resin manufacturer’s range
- Check relative humidity and dew point to avoid condensation on pipes
- Use heating blankets in cold weather but never place them directly on the floor or fold them
This is especially important during outdoor fiberglass pipe installation.
OTA Fiberglass Heating Blankets are engineered for controlled, uniform heating during GRE/FRP lamination. Available in a wide range of pipe sizes (from 1″ to 48″), these blankets come with an integrated temperature controller, ensuring proper resin curing even in harsh or cold environments.
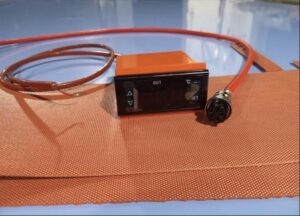
Correct Use of Pipe Shavers
For GRE installations, use a pipe shaver to create a tapered spigot end:
- Fit the expandable O-ring arbor into the pipe for a secure hold
- Set the shaving depth and length precisely to expose clean laminate without overcutting
- Power the shaver using the OToAworks 230V motor unit or manual drive where applicable
- Clamp the pipe securely using a pipe vise to prevent movement
This ensures precise GRE GRP tapering, which is key to achieving reliable bonds.
For optimal results, consider using the OTA Fiberglass Pipe Shaver a high-precision tool designed specifically for GRE/FRP pipe tapering. Its adjustable tapering depth and consistent shaving output ensure maximum bond integrity while minimizing the risk of over-shaving or pipe damage.
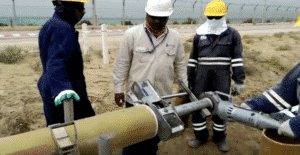
Safe and Consistent GRE FRP Lamination Practice
Once surfaces are prepared and conditions checked:
- Use pre-cut glass mats (woven roving, chopped strand mat, etc.)
- Apply resin with brushes or rollers in layers, removing air bubbles with a laminating roller
- Follow the correct layup schedule and overlap
- Allow partial curing between layers, sanding lightly to maintain bonding strength
Timing between layers is critical, ideally; the next layer should follow within 1 hour of curing.
Heat and Fire Safety During Curing
Resins generate heat during fiberglass pipe curing (exothermic reaction). Always:
- Use insulated gloves when handling recently laminated joints
- Monitor heat using thermocouples or infrared thermometers
- Keep flammables away from the work zone
Do not leave heating blankets unattended and never cure near open flames or sparks.
Post-Lamination Inspection and Documentation
After curing:
- Visually inspect the lamination for blisters, delamination, cracks, or dry patches
- Tap-test for voids or poor adhesion
- Confirm curing time is complete before pressure testing
- Document lamination batch numbers, installer names, and curing conditions for traceability
If defects are found, grind and re-laminate using the proper repair procedure.
Conclusion
Laminating GRE and FRP pipelines in the field involves more than technical know-how—it requires a safety-first mindset at every stage. From PPE and resin handling to environmental control and curing protocols, each step is essential for both installer protection and system integrity.
By following these safety tips, field teams can reduce health risks, prevent costly rework, and deliver high-quality, long-lasting joints that perform under demanding service conditions. These practices are essential for successful GRE FRP lamination, especially in mission-critical applications.
Learn More About Us
Reengineer Value